IR-reflective pigment formulations significantly reduce the surface temperature of facade cladding.
The heat-optimized coloring of sidings with the use of IR-reflective pigment mixtures and masterbatches is an economical and clever way to protect your facade claddings from an excessively high surface temperature and therefore from deformation or warping. This is the result of an intensive development process which we have been driving forward for several years together with sidings manufacturers and suppliers of raw materials.
Development according to the market requirements.
Sidings are particularly popular in the USA, Poland and Russia, as they represent a comparatively economical and esthetically appealing option for facade cladding. A challenge that arose for the first time in Turkey, before being followed by the Russian market, the problem of heating PVC surfaces has become increasingly important for European sidings manufacturers. To counteract unwanted secondary phenomena such as distortion, discoloration and combustion, we embarked on developing and completing intensive research into the possibilities of IR-reflective coloring, especially for dark hues, as long ago as 2004. For this purpose, we have evaluated a large number of pigment groups which have proven to bring about a significant reduction in the temperatures of sidings surfaces.
Reflecting instead of absorbing.
To reduce the temperature increase on a surface, it is necessary to maximize the amount solar energy from the sun which is reflected back from the siding surface. The TSR value (total solar reflectance) gives information about the solar reflectivity of a pigmented surface. The greater the TSR value, the more strongly the solar radiation is reflected, and the less the measurable temperature increase.
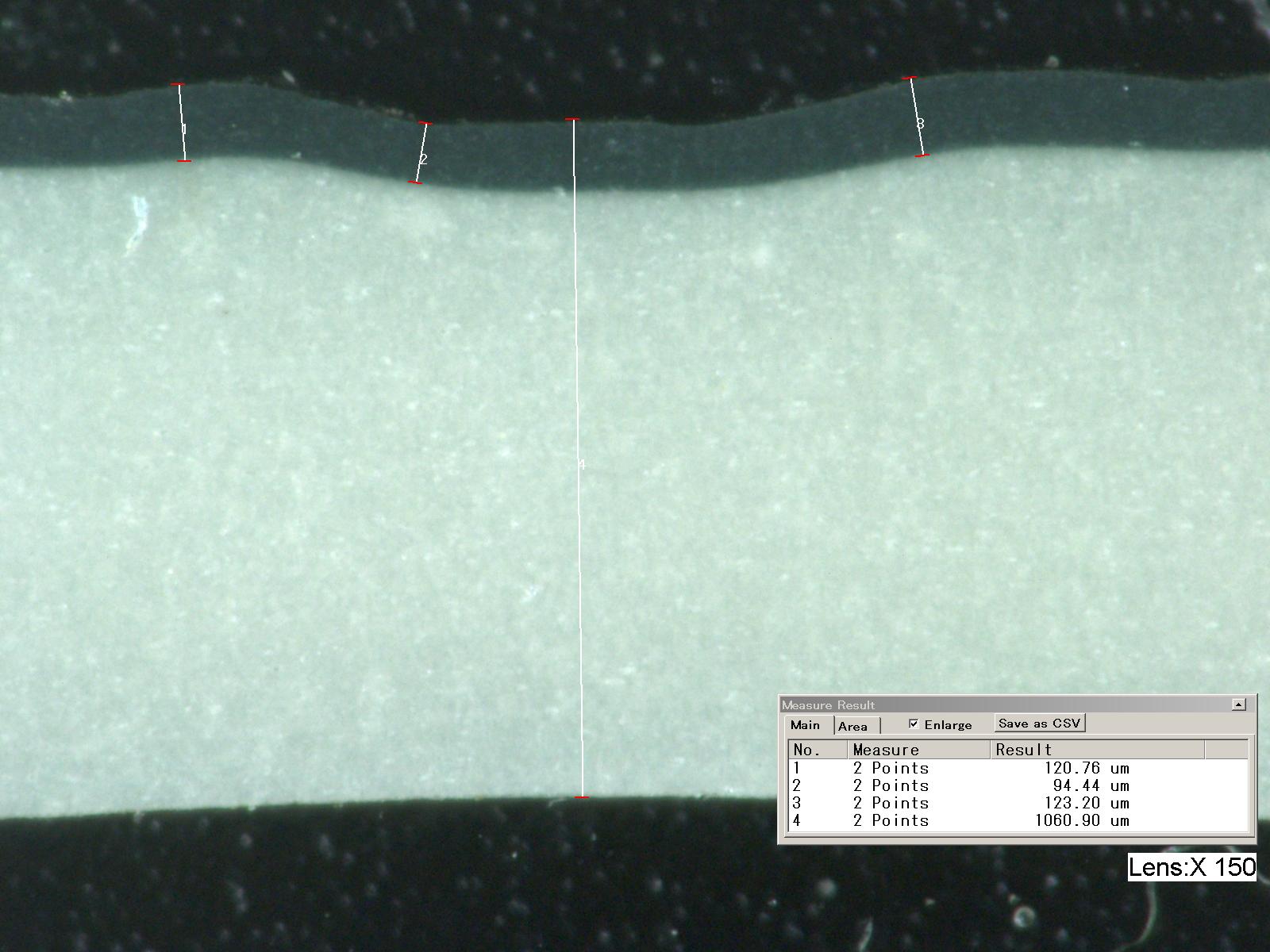
Microscope image of a co-extruded PVC siding cross-section.
A question of the right formulation.
As cool as possible, but still very light-stable for good color retention – in combination with the color requirements and the requirements surrounding dimensional stability, a multiplicity of different TSR plus pigment formulations results. In this respect, it is important to remember that effective IR reflection cannot simply be achieved with the addition of special additives. The substitution of carbon black is not a panacea either, as it is associated with considerable challenges in terms of coloring and the required light and weather fastness.
The key is in the targeted selection of pigments which have the lowest possible absorption in the infrared range. Only in this way is it possible for low surface temperatures to be achieved with dark, gray or bright shades of color. Identifying these and transferring them to a customer-specific formulation is a key task in configuring the heat-optimized color formulation.
Heat-optimized coloring of sidings with masterbatch: considerable demands on the support material.
It is necessary for the colorant and support material to match. Therefore, over the course of many years, we have developed a PVC-based support material system which can be optimally processed with the heat-optimized and color-fast pigments for PVC sidings. And there are no side effects at higher application concentrations either. Rapid and straightforward changes in color are possible without any problem.
With light shades of color, the base white pigmentation is often already included in the PVC mixture. Here, we work with application concentrations of 1.5% to 3.0%. For dark shades of color with 6% PVC masterbatch and over, which can only be realized technically with a well-matched PVC support material.
Even more flexible thanks to co-extrusion.
Sidings are rarely created as a full profile, but generally two-layered. The base coat is made of PVC and comparatively cost-effective colorants. The top coat, by contrast, is directly exposed to the sun, wind and weather. It is the actual useful layer which is required to withstand all stresses. As a result of this, especially high-quality PVC formulations and precolor® microgranulate based on PVC are used here, which are processed in the co-extrusion process.
A colorless PVC plastic mixture is generally used which is added to the PVC masterbatch to give the color online, i.e. directly at the extrusion line using dosing equipment. Because of the frequent color changes in the siding area, this is a practical and economical necessity.
The bottom line:
Heat-optimized pigment formulations are an efficient way of limiting the heating of siding surfaces. This can prevent deformations and damage caused thereby. A temperature-dependent discoloration or burning of the profile surfaces is also avoided. With this effective coloring technology, it is possible to significantly extend the service life of PVC sidings.
Your personal contact: Carsten Herrmann
Do you have any further questions about the coloring of your sidings, or would you like to start a project with us? We’re happy to help.
Phone +49 9232 9945-46
Mobil +49 172 7905845
E-mail carsten.herrmann@farbenwerke.de
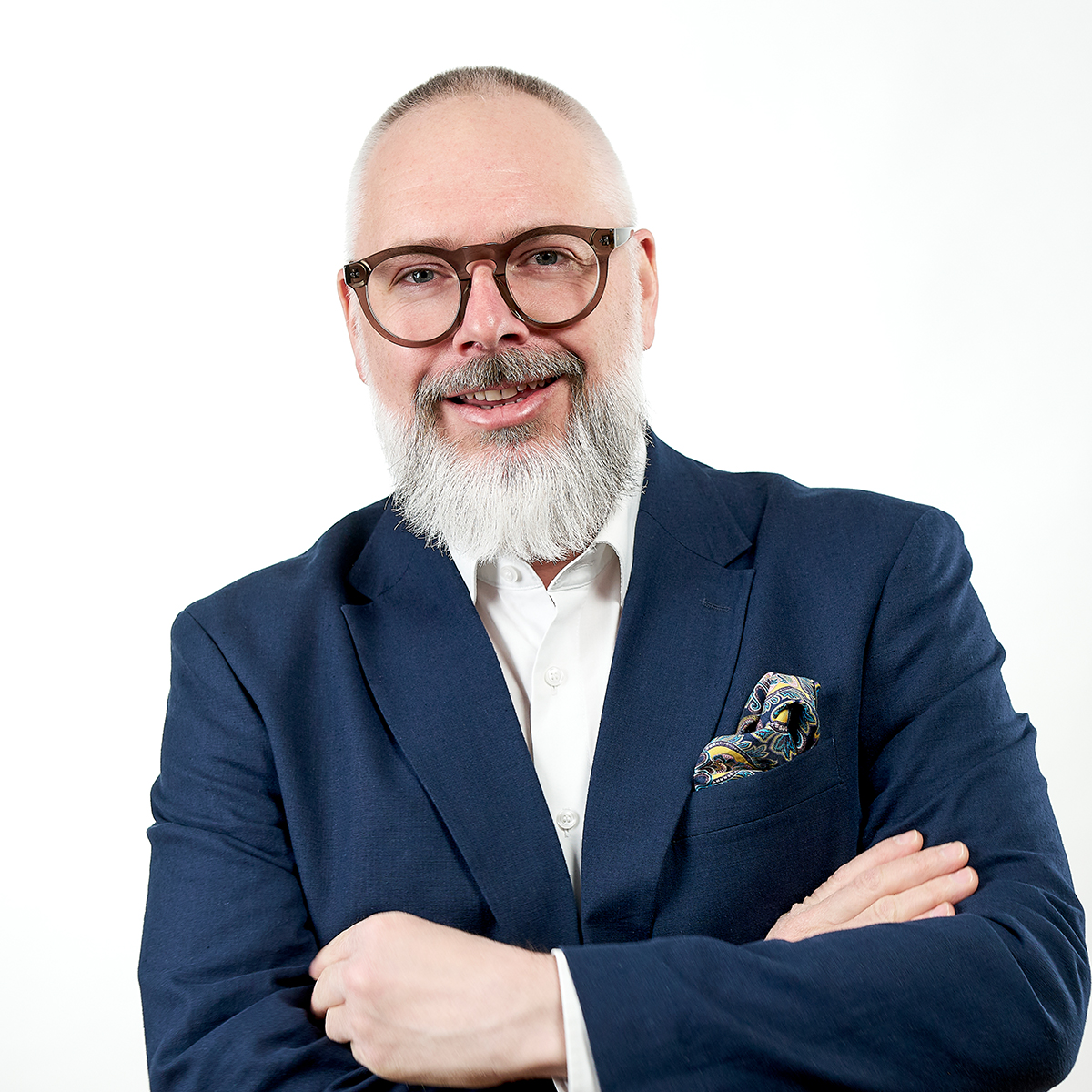